Inks can be one of the most innovative products of all time. For thousands of years, inks have been used to tell stories. Caves all around the world showcase the artwork of our ancient ancestors. Inks can also show a brand’s story in a wide variety of precise colors.
Thanks to technological advances, inks are now known for functionality instead of storytelling. Technology has consistently gotten smaller over the years. One main reason for the shrinkage is the use of functional inks mixed into precision printing processes.
The two main kinds of inks used at BTI are UV and Solvent inks. Both have advantages, but they are relatively similar too. Both inks can be printed onto a broad variety of substrates and materials.
What’s the difference between UV and Solvent Inks?
What is UV ink?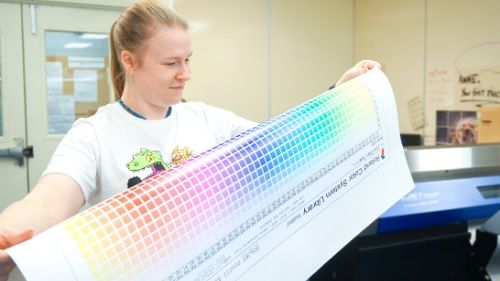
To break down the definition, UV stands for UltraViolet. Sadly, ultraviolet isn’t the color of these inks, it would be ultra-cool if it were though. UV refers to how the ink gets finished or cured.
Once the ink is printed onto the material, ultraviolet lights flash to rapidly cure the ink into place. Inks that are involved in UV printing are instantly dried before the printing operator has to handle them.
Since the ink only dries under UV light, printers do not have to worry about the ink becoming too thick or start to dry while still on the screen. UV ink is also popular because it is a greener and more sustainable option.
There are no Volatile Organic Compounds or VOCs associated with UV cured ink. This can also mean that disposing of this kind of ink is easier. Many printers believe that UV ink is better for finely detailed projects. Products designed with UV inks can also provide a higher gloss.
What is Solvent Ink?
Solvent-based inks are pretty easy to understand too. The solvent in these kinds of inks is what adheres the ink to the material below. Solvent creates a chemical bond between the ink and the material that it’s being printed on.
The mixing process uses water or liquid, some pigment added for color, and some kind of resin or solvent to make it all stick creates solvent-based inks.
Solvents can also be cured by air or more commonly heat. It is more popular for solvent inks to be cured by heat because it can be quicker than letting the solvents evaporate.
Once all of the solvents are gone the pigment left behind is a hardened long-lasting shell. While solvent ink dries it becomes smaller, causing the printers to use more ink than the UV counterpart. Estimates predict that up to 40% of solvent ink gets evaporated.
Technology advancements have lead to the creation and use of eco-solvent printing. BTI currently uses one digital eco-solvent Roland printer. The most popular substrate for solvent inks to be printed on is acrylic.
Solvent ink gets used in an extensive assortment of products, but most often used in our printed electronics product line.
Conductive Inks
Some of the more popular solvent-based inks that are used at BTI are conductive inks. Printed electronics or PE would not be possible without the use of conductive inks. These kinds of inks can be organic or metallic. Functional inks are created by adding conductive particles such as carbon, silver or copper, into a solvent based solution. When the ink is cured the solvents bake off and the conductive particles remain to create circuitry.
PE products like biometric sensors and flex heaters need conductive inks to function. These product’s stack-ups are layered with carbon and silver inks to allow electricity to flow throughout the circuit.
Dielectrics & Encapsulants
Other solvent-based inks are dielectrics and encapsulants. These inks are nonconductive and help to insulate the conductive layers from one another. This protective encapsulant can make wearable electronics last longer by protecting it from the environment, wetness, and debris.
User wearable products like biometric sensors and flexible heaters also use silver conductive inks to make the product as thin as possible. Jamie Orlando, a member of the BTI team commented that;
“The conductive particles in the solvent begin to come in close contact with one another as the solvent evaporates. The particles become closer together and less resistant. That’s why PE is tricky. You need to measure the ink deposition thickness and resistance AFTER the solvent has been baked to determine if it will work for the application.”
10 Key differences between UV-cured and Solvent-based inks
- UV print projects are ready to move and ship as soon as it gets off the press.
- UV print products can contain a very sharp image with exceptional detail and a deep variety of colors.
- User interface products like decals and graphic overlays typically use UV inks.
- The solvent inks require a ventilation system, unlike the safer alternative of UV printing.
- The solvents in inks can also be toxic, and many UV inks are eco-friendly.
- Eco-solvent inks are popular for being more sustainable for the environment.
- When engineering PE, measurements are needed after the solvent is cured onto the substrate.
- Conductive Inks can be printed on polyurethane, which allows electronics to be flexible.
- Conductive inks like silver and carbon can add functionality to wearables and other PE products.
- When designing PE, dielectrics and encapsulants can add protection and durability.
Meet the Author
Ashley Foster is a graduate of Slippery Rock University, where she earned her Bachelor’s degree in Business Administration, majored in Business Management and minored in Marketing. While Ashley was studying at SRU she found a passion for marketing. Although she is busy working, she spends her free time traveling and hiking with friends. She is also a volunteer for the American Marketing Association, Pittsburgh Chapter, and an active alumni member of FCCLA.